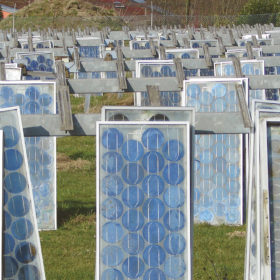
In February, non-profit EU solar panel recycling body PV Cycle announced it had collected 5,000 tons of modules in France, of which 94.7% could be recycled. A reader asked us about the remaining 5.3% and here, PV Cycle’s communications manager, Bertrand Lempkowicz, responds.
Last year, 5,000 tons of solar modules were collected for recycling in France. That figure could hit 50,000 tons by 2030, EU-funded panel recycling body PV Cycle has predicted. Europe-wide, the organization had collected more than 27,000 metric tons of modules by the end of 2018, demonstrating the management of solar waste and recycling of panels with a 25-year lifespan, is of paramount importance.
EU regulations require 85% collection and 80% recycling of the materials used in PV panels, under the Waste Electrical and Electronic Equipment (WEEE) Directive, which was extended to solar products in 2012.
At 94.7%, the recovery rate of a crystalline silicon-based PV module already exceeds those levels, says PV Cycle. The industrial plant which makes it possible to achieve that rate is in Rousset, in the Bouches-du-Rhône region of France. The facility is operated by Veolia and said to be the first industrial plant of its kind.
Made up of aluminum, glass, plastic, copper, silver and silicon, solar panels are cut and crushed after the frame, cables and junction box have been removed. The components are separated and sent to separate recycling streams.
‘Exceptional’ recycling
“Ninety-five per cent is an exceptional recycling figure, especially for a multi-component product,” PV Cycle communications manager Bertrand Lempkowicz told pv magazine France. “Only soda cans can claim to do better but they don’t reach 100% either. A washing machine doesn’t come close to 70% recycling, everyone has one but nobody cares.”
What about the 5.3% of solar panel components that is not recycled?
“The non-recycled materials are mainly dust trapped in the filters after shredding,” said Lempkowicz. “They don’t count [as part of a solar panel], but these filters will also be recycled. The dust can also be incinerated or used as a substitute for sand in construction, since glass, silicon and silicone are all derived from sand.
“The backsheet – the vinyl sheet on the back of the panel used to insulate the components – will be energy recovered. The EVA [ethyl vinyl acetate] or tedlar used [in backsheets] could be used as a binder for paint but this would require cleaning. It is actually more environmentally friendly to incinerate it (in a filtered incinerator) than to use tons of water to clean it” – thus demonstrating the cross-sectoral nature of solar module recycling.
Business model
Although it is now possible to technically upgrade a panel by almost 95%, it remains difficult to find a business model to support the operation. The volume of panels awaiting recycling remains low, for now, rendering the process unsustainable for the time being. “PV modules are relatively new products, the first installations of which are not yet at the end of their life cycle,” said Lempkowicz, who added: “The current waste is mainly due to breakage. However, these volumes will be much higher in about ten years’ time.”
To solve the techno-economic conundrum, European-funded programs such as Circusol (Circular business models for the solar power industry) and Cabriss (implementation of a circular economy based on recycled, reused and recovered indium, silicon and silver materials for PV and other applications) have been established to formalize reuse, repair and remanufacturing value chains in the PV industry.
David Pelletier is project leader at the Institut national de l’energie solaire (INES) of the French government Commissariat à l’énergie atomique (CEA). Luc Federzoni is in charge of strategic programs at the latter. Both agree on the importance of ramping up eco-design in the PV sector, to anticipate, well in advance, remanufacturing or recycling of a new generation of modules and to create 100% recyclable cells and panels.
Circular economy
The July edition of pv magazine focused on circular manufacturing, a large component of which concerns recycling, although, as aforementioned, reuse, repair, remanufacturing and repurposing are expected to play key roles in future. Pelletier and Federzoni want to develop a circular economy model based on PV waste manufacturing and end-of-life modules for reuse in the solar sector or other industrial sectors, they said.
“We managed to develop all [the] technologies required to separate, purify and recycle PV waste manufacturing and end-of-life modules,” the two stated. That is achieved by opening modules with non-thermal processes to recover materials. However, the duo admitted it is currently “difficult” to find profitable business models when recycling volumes are still small.
Increased activity
While the EU is the only region to have adopted a clear regulatory framework supporting PV module recycling, other locations, including the United States, Australia and Asia, are ramping up activity, given the large volumes of waste looming and the continued pace of PV deployment.
A report released by the International Energy Agency’s Photovoltaic Power Systems Program in January 2018 – End-of‐Life Management of Photovoltaic Panels: Trends in PV Module Recycling Technologies – reported 178 PV recycling patents had been filed. Of those, 128 focused on crystalline silicon (c-Si) technology and another 44 were for compound technologies, including thin film modules. Almost half the patents originated in China, although increased activity had been witnessed in Korea and Japan at that point.
Look out for more on this topic in our next UP Initiative quarterly theme, which will focus on PV module recycling. Email up@pv-magazine.com for more details.
Lắp đặt điện mặt trời Khải Minh Tech
https://ift.tt/2X7bF6x
0906633505
info.khaiminhtech@gmail.com
80/39 Trần Quang Diệu, Phường 14, Quận 3
Lắp đặt điện mặt trời Khải Minh Tech
https://ift.tt/2ZH4TRU
Không có nhận xét nào:
Đăng nhận xét