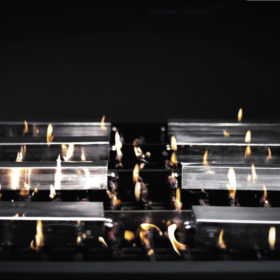
With demand for lithium-ion battery cells picking up, largely driven by EVs but also from the fast-growing stationary storage segment, production capacities in China are ramping up quickly. But safety and quality must remain centrally important in the face of the need to scale, even more so after the numerous battery fires that shocked buyers globally and brought the South Korean market to a standstill. Clean Energy Associates (CEA) has launched the 2019 BESS Supplier Market Intelligence Program report, covering 40 suppliers, in an effort to support buyers navigating this novel supplier landscape. George Touloupas, CEA’s director of technology and quality for solar and storage, shares the company’s key findings on the supply chain and tells us what can have an impact on Li-ion safety and reliability.
From pv magazine 12/2019
As outlined in CEA’s 2019 Battery Energy Storage Market Intelligence Program report, the battery energy storage landscape is continuing to evolve. While battery manufacturing was once dominated by Japan and more recently South Korea, China is quickly becoming a major player. Nowhere is this more apparent than with lithium-ion batteries (LIB). With massive LIB manufacturing capacity online and hundreds of GWh planned through 2021 (see chart on p.75), economies of scale along with technology improvements will further drive down the price of lithium battery cells, which have already fallen around 85% since 2010.
Chinese manufacturers plan to lead this expansion, and their control of the value chain, coupled with favorable policies for new energy vehicles, are designed to propel them to the top of the supply chain.
According to CEA’s analysis of various data sources, global annual demand for lithium-ion batteries is expected to exceed 2,000 GWh by 2030. While most of this demand is projected for EVs, an expected 5%-10% will be for stationary battery energy storage systems (BESS). Grid-connected battery systems providing grid services is a relatively new application, with frequency regulation in the United States and later the United Kingdom being the forerunners. A broad spectrum of applications is being explored around the globe and as BESS costs drop, more use cases will become viable, both in front of and behind the meter, such as gas peaker replacement, renewable firming, load shifting, capacity services, grid inertia, demand charge avoidance, self-consumption, backup services, and investment deferrals. At much higher levels of renewable penetration, other storage technologies that are better suited for long duration and low cost will be introduced. But for the time being, lithium ion seems to be the leading technology, as its adoption by the EV industry brings the benefit of mass scale that can achieve low cost and standardization.
The numerous battery fires that shocked buyers globally and brought the South Korean market to a standstill have instilled a new focus on quality and safety that goes beyond relying on warranties backed by balance sheets and depending on a very small group of suppliers. A more holistic due diligence, starting from upstream in-factory battery cell quality control and going all the way down to system design and fire protection, is becoming mainstream practice.
Battery chemistries
The choice of lithium-ion chemistries suitable for large-scale BESS can lead down many paths. But although the lithium-ion battery chemistry “zoo” has many variants (LMO, LTO, LCO, NCA, NCM, and LFP), only nickel-cobalt-manganese (NCM), nickel-cobalt-aluminum (NCA, only used by Panasonic and Tesla), and lithium-ferrous-phosphate (LFP) have achieved mass scale for BESS.
The predominant chemistry is still somewhat geographical in nature. For the South Korean suppliers, NCM is the main chemistry of choice for BESS and has an expected annual manufacturing capacity of 54 GWh by the end of 2019. In North America, Tesla’s Gigafactory 1 has 34 GWh of annual manufacturing capacity of Panasonic NCA 21700 cylindrical cells, primarily for Tesla’s EV products.
Chinese suppliers have a significant manufacturing capacity for both NCM and LFP (see chart p.73), as well as some NCA, and the production lines can be switched relatively easily between chemistries. LFP’s intrinsically safe nature, due to its reduced thermal runaway risk, led to its mainstream usage in China, as it was considered more suitable for e-mobility. However, as energy density is the single most important factor in achieving longer ranges for EV, a shift has occurred in China toward the more energy-dense NCM chemistry. Even so, for electric buses – a big market within China – LFP batteries are mandatory due to safety reasons. LFP remains the chemistry of choice for Chinese BESS suppliers, who offer LFP cells with longer lifecycles than NCM cells. Importantly, LFP cells do not contain cobalt, and have an inherently more stable cost roadmap. The instability of the cobalt supply chain, mainly due to 60% of global supply being sourced from the Democratic Republic of Congo, is a key factor in recent price hikes of NCM chemistry batteries. Finally, Chinese suppliers would be very reluctant to provide large scale BESS with NCM, as they are concerned with the increased thermal runaway risk in large systems.
For LFP, the lower energy density does create a balance of plant cost disadvantage, but the more stable and lower cost raw material prices, higher cycle life, and the reduced risk of thermal runaway make it a chemistry that certainly has a future in energy storage. As a simple rule of thumb, Chinese BESS will be strictly LFP, and South Korean will be strictly cobalt-based (NCM).
CEA’s report also covers alternative battery chemistries, such as NGK’s NaS battery, which has a significant track record, and vanadium redox flow batteries from two large Chinese suppliers. These chemistries have an advantage in long-duration applications, although lithium-ion batteries keep pushing the duration envelope as costs come down. Altairnano’s lithium titanate chemistry has also been labeled “alternative,” as it is only suited to high charge/discharge rate, high cycling, and special applications. CEA will keep monitoring this space as well as new entrants gain traction.
Safety and quality
By early 2019, 23 BESS fires had been reported in South Korea, coinciding with a tremendous 4-5 GWh installation rush in 2018. The Ministry of Trade, Industry and Energy (MOTIE) put the brakes on new installations and severely restricted the operating conditions of existing ones. MOTIE then conducted a six-month long investigation, published in June 2019, identifying as probable causes insufficient protection, inadequate environment conditions oversight, faulty installations and sub-standard integration. MOTIE also proposed additional requirements on battery and PCS manufacturing quality, installation, O&M, and firefighting. CEA has prepared a white paper about the fires, available to clients, with a translation of the report and analysis of the findings, identifying potential gaps in the investigation of the root causes.
Investors are highly concerned, as the South Korean BESS supply chain had been considered one of the most technologically advanced globally. Investors realize that this is still a nascent industry and a lot remains to be done regarding independent oversight across all stages of production and integration.
BESS quality assurance is a relatively new field, as the volumes have been small in the past and the supplier pool was very restricted, with buyers relying almost entirely on brand and balance sheets. However, as independent oversight becomes imperative, CEA’s audit data reveal a more complex reality. At the battery cell level, defective coating and folding of the electrodes can both present a fire risk and reduce the battery’s life. Cell, module and rack level protections must be in place and fully functional during testing, or safety risks will occur.
System factory acceptance tests must be independently performed, and they must be exhaustive, covering both performance and safety aspects. And system design and warranty structures must be analyzed and assessed by third parties to help protect buyers from safety or underperformance risks and to assist them in understanding the cost structure of the offerings.
By 2019, the group of the four major Chinese suppliers will have a combined capacity of 135 GWh and the group of the four major international suppliers will have 119 GWh. In 2021, the planned combined capacities will be 230 GWh and 250 GWh respectively. The minor Chinese cell suppliers will have 140 GWh in 2019 and 227 GWh in 2021 (see chart below left). The bold dynamic of the Chinese cell makers, boosted by aggressive players such as CATL and BYD and the steep growth of EVs, is clearly placing them in a very strong position to threaten the supremacy of the incumbent small club of the big four: Panasonic, LG Chem, Samsung SDI and SKI.
Although one can still argue that the Chinese suppliers may be technologically less advanced than the big four international suppliers, their focus on the LFP chemistry and development of BESS specialized cells (CATL and others), and their R&D spending as a percentage of revenue (see chart above), enables them to challenge the status quo.
As BESS installations are expected to see a tenfold increase over the next six years, it is imperative for buyers to diversify their supply chain, learn how to comprehend and navigate the complexities of the Chinese supply chain, and implement the right mixture of due diligence and oversight.
About the author
George Touloupas is the director of technology and quality for solar and storage at Clean Energy Associates, a firm that focuses on solar PV quality assurance, supply chain management, and engineering services (https://ift.tt/2Dt78le). At CEA he leads projects centered on developing CEA’s internal quality standards, researching new production technologies, and developing new services. He has an extensive background in PV manufacturing, as well as downstream experience. Prior to joining CEA, he served as the chief operating and technical officer at Philadelphia Solar in Jordan and as technical and operations director at Recom.
Lắp đặt điện mặt trời Khải Minh Tech
https://ift.tt/2X7bF6x
0906633505
info.khaiminhtech@gmail.com
80/39 Trần Quang Diệu, Phường 14, Quận 3
Lắp đặt điện mặt trời Khải Minh Tech
https://ift.tt/2ZH4TRU
Không có nhận xét nào:
Đăng nhận xét