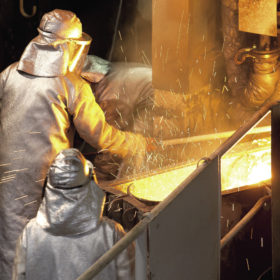
Design-for-recycling is not perceived to be high up the list of priorities for battery manufacturers but solutions do exist. Lithium-ion device recycling is technically feasible but requires an improvement in its business case to take off.
The mounting challenge of lithium-ion battery recycling should be addressed at the design stage. To date, though, manufacturers have focused more on safety, power density, and cyclability.
Lithium-ion battery recycling researchers from the universities of Leicester, Newcastle and Birmingham; The Faraday Institution; the ReCell Center and the Argonne National Laboratory have examined product design and published their findings in the paper The importance of design in lithium-ion battery recycling – a critical review, published in Green Chemistry.
“To create a circular economy for any material, it is important to have few components, a lower cost for the secondary process [recycling] than the primary process [raw material extraction], a simple purification flowsheet, valuable components, and a collection and segregation mechanism,” wrote the authors. “It also helps when the material has a significant environmental impact if not recycled, as this tends to mandate its recycling.”
Lead-acid
Lead-acid batteries fulfill those design requirements, which explains a collection rate of near 100% in Japan, the U.S. and most of Europe and a recycling regime which recovers more than 98% of the total mass of the batteries. Lead-acid batteries are straightforward in design, with a polypropylene casing, an electrolyte, and two electrodes, made from lead and lead oxide. Separating components by density is relatively simple given lead and polypropylene have values of 11.3 and 0.9g/cm-3.
The similar density values of the cathodes and current collectors in lithium-ion batteries renders a similar approach impossible. Therefore, lithium-ion devices require approaches such as redox reactions, solubility, or exploiting electrostatic and magnetic properties to separate the materials of which the cells are made up.
Lack of labeling is another significant obstacle to an effective recycling regime. Unlike lead-acid batteries, lithium devices show a variety of chemistries and architectures, such as NCA, NMC, LMO, LCO, and LFP batteries, all of which can combine in different chemistries. Cells can also come in pouch, prismatic, or cylindrical form before being soldered together into modules and combined in the pack.
Costs
The U.K.-U.S. research group said there are no global standards for battery labeling, which is needed to clearly indicate device composition to recyclers. As a result, hydrometallurgy – which involves shredding and acidic treatment; and pyrometallurgy, highly energy-intensive smelting before the acid step, have become commonplace in lithium-ion battery recycling. Hydrometallurgy requires pre-treatment, discharging, and correct dismantling rather than ‘comminution' – crushing or shredding.
Handling and any pre-treatment could be carried out by robotics, but only if battery type and architecture is clearly labeled, according to the authors of the study. The researchers said global auto engineer industry body SAE International recently recommended a labeling scheme. With NGO Greenpeace East Asia today calling on China to put second-life battery use and recycling at the heart of its 2060 zero-carbon plan, the authors of the lithium-ion recycling paper said Beijing is considering labeling standards for lithium devices.
The variation in how cells and modules are arranged within battery packs – sometimes within a single EV manufacturer fleet – present another hurdle for recyclers. Lithium-ion devices are organized to maximize safety and cell longevity at the expense of recyclability.
The higher the cell count, the lower the proportion of active – and valuable – materials to battery weight. Increased cell count also complicates the opening and separation steps which add to recycling costs. A Tesla Model S electric vehicle (EV) with an 85 kWh battery pack contains 16 modules, each comprising 444 cells – 7,104 cylindrical cells in each car. A BMW i3 features 96 prismatic cells; a Nissan Leaf 192 pouch cells.
“When dismantling is slow and costly the only method of recycling becomes pyrometallurgy, which is expensive and inefficient,” wrote the authors of the Green Chemistry paper. “Recycling is therefore in a ‘catch 22' situation, where cell and pack design controls recycling strategy.”
Manual disassembly of packs and modules to extract individual cells is the preferred option to recover pure materials but takes longer than comminution. Such delays are exacerbated by the myriad combinations of cell and pack design which make automated disassembly virtually unattainable.
The paper's authors suggest standardization of outermost-layer fixings and module and cell arrangements to overcome the problem, in another echo of Greenpeace East Asia's recommendations for the Chinese battery industry. Packs could be closed with screws, push-fit arrangements, or other torque mechanisms for which a standard tool would permit access with relative ease and without damaging the layers beneath.
Solid busbars
Batteries could also feature solid busbars rather than the flexible cables that connect modules at present, said the researchers. Such structures could see cells connected directly to the busbar without the need for a module and robots could more easily detach cells from the busbar. Cell components could be more easily accessed and separated with the addition of a break point or other opening mechanism.
The academics also suggested focusing on the, currently non-reversible binding agents which attach active materials to the polymer layer in lithium-ion devices. Dealing with conventional binders drives up the costs of separating cathode and anode materials from the polymer.
“[A] design-for-recycle [approach] often involves minor changes to product structures but can help to establish a circular economy if it returns raw materials to the manufacturing process at a significantly reduced cost compared with primary sources,” added the authors of the paper.
Solutions
The researchers said separating electrode materials without shredding could drive down the cost of recycling to up to 70% cheaper than the expense of sourcing virgin materials. Comprehensive labeling, simplified solid-bulk architectures, easy-to-open design, and reversible adhesives and binders would solve the lion's share of lithium-ion battery recycling issues, said the U.K.-U.S. group.
The academics also suggested how to bring in such regulations, suggesting extended manufacturer responsibility and an obligation to take back end-of-life products would propel engineers to adopt a design-for-recycling approach.
Circular manufacturing
Circular manufacturing was the focus of the pv magazine UP initiative’s Q3 theme. We considered whether adopting a circular approach could create a competitive edge and reap financial and reputational rewards, and we examined what is already being done in the solar industry. Browse our coverage here.
Lắp đặt điện mặt trời Khải Minh Tech
https://ift.tt/2X7bF6x
0906633505
info.khaiminhtech@gmail.com
80/39 Trần Quang Diệu, Phường 14, Quận 3
Lắp đặt điện mặt trời Khải Minh Tech
https://ift.tt/2ZH4TRU
Không có nhận xét nào:
Đăng nhận xét