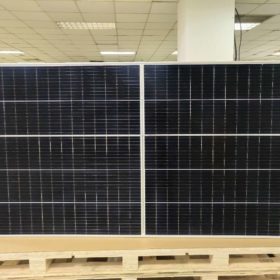
In the second article in a series, pv magazine editor Pilar Sánchez Molina and industry experts keep discussing the challenges and opportunities created by new panels with power output exceeding 500 W.
How did we get here?
The manufacturing process based on the wafer sizes of 156mm by 156mm (M1) and 156.75mm by 156.75mm (M2), which became standard in 2017, barely changed until about 2018 and traditional manufacturers have invested many resources in production lines based on this manufacturing process over the past years.
By contrast, new entrants in the solar manufacturing business may benefit from the “late-mover advantage”, which means they can acquire new production lines that result in more efficient modules without having to wait to amortize other older lines.
To address this competitive advantage, one of the traditional manufacturers, Jinko, introduced a module with larger cells (158.75mm by 158.75mm) with a relatively small investment in the second half of 2018. As the cell size increased, the resulting power increased proportionally, without implying an improvement in the module technology itself.
Other manufacturers decided to follow Jinko’s strategy until monocrystalline module specialist Longi made a master move by releasing, in April 2019, a module with 166mm by 166mm cells, incompatible with the old lines, and thus distancing itself again from the rest of the solar producers. This forced competitors to invest a notable capex in order to launch the same module on the market. More capex, higher price, less competitiveness.
At that point, a world leader in wafer production for the semiconductor industry came into play, Zhonghuan Semiconductor, which, in September 2019, launched an even larger cell, the M12, measuring 210mm by 210mm and based on 12-inch wafers, more typical of the aforementioned semiconductor industry.
It was this innovation that most consistently introduced the concept of “half-cut” and “third-cut cells”, two concepts that respond to the need to reduce cell currents due to the wafers’ large site. Why? Asier Ukar, from PI Berlin, explained: “More surface, more current. More current, more losses as long as the busbar section must be kept constant (which is what would be done to avoid increasing costs). So what can be done to cut losses without investing in higher section busbars? Well, split the cells in two or three so that the current per busbar is reduced (the series losses increase and decrease exponentially with the current). In this way, larger modules can be manufactured without the higher series losses reducing the efficiency of the module. And yet the currents are greater than they were.”
A company that does not wish to be mentioned added another reason: “Manufacturers are not very clear about what can happen to the module if very high currents flow, possible degradation or disruptive phenomena are not ruled out, therefore they reduce them as a precaution.”
But it doesn’t end here: Longi, Jinko and JA Solar have launched modules with 182mm by 182mm cells on the market this year to compete against the M12. The advantage of these modules is that they conform well to the standard layout of the 60-cell module (or 120 if they are split) and therefore do not introduce unusual dimensions that generate headaches for manufacturers of mounting structures or trackers.
The largest and most powerful module manufacturers can announce loudly that their production capacity in MW or GW is increasing. Manufacturing a 600 W module costs you the same time as manufacturing a 420 W one, with which you can get much more power in the same time and thus reduce specific operating costs in $/Wp, respondents explained. In other words, it represents a saving for the manufacturer which, by the way, is not reflected in the cost of the module. “Very smart,” they agreed.
Lắp đặt điện mặt trời Khải Minh Tech
https://ift.tt/2X7bF6x
0906633505
info.khaiminhtech@gmail.com
80/39 Trần Quang Diệu, Phường 14, Quận 3
Lắp đặt điện mặt trời Khải Minh Tech
https://ift.tt/2ZH4TRU
Không có nhận xét nào:
Đăng nhận xét